The Internet of Things (IoT) is helping shape the future of business through mass access to data from previously untapped resources. Currently, there are an estimated 20 billion connected devices, and this is predicted to grow to 50 billion by 2020. The possibilities it creates (via analytics and augmented reality experiences) for businesses, across a variety of industries, is growing.
>See also: IoT and manufacturing: more than streamlining the factory process
At LiveWorx 2017, hosted in Boston, PTC – the global provider of technology platforms (and organiser of the event) – highlighted the huge potential for growth and open innovation that the IoT offers. In a quite dazzling opening to the conference, Jim Heppelmann – president and CEO of PTC – described how the IoT is transforming the traditional. Specifically, how the technology is converging the physical and digital spheres, in order to generate value.
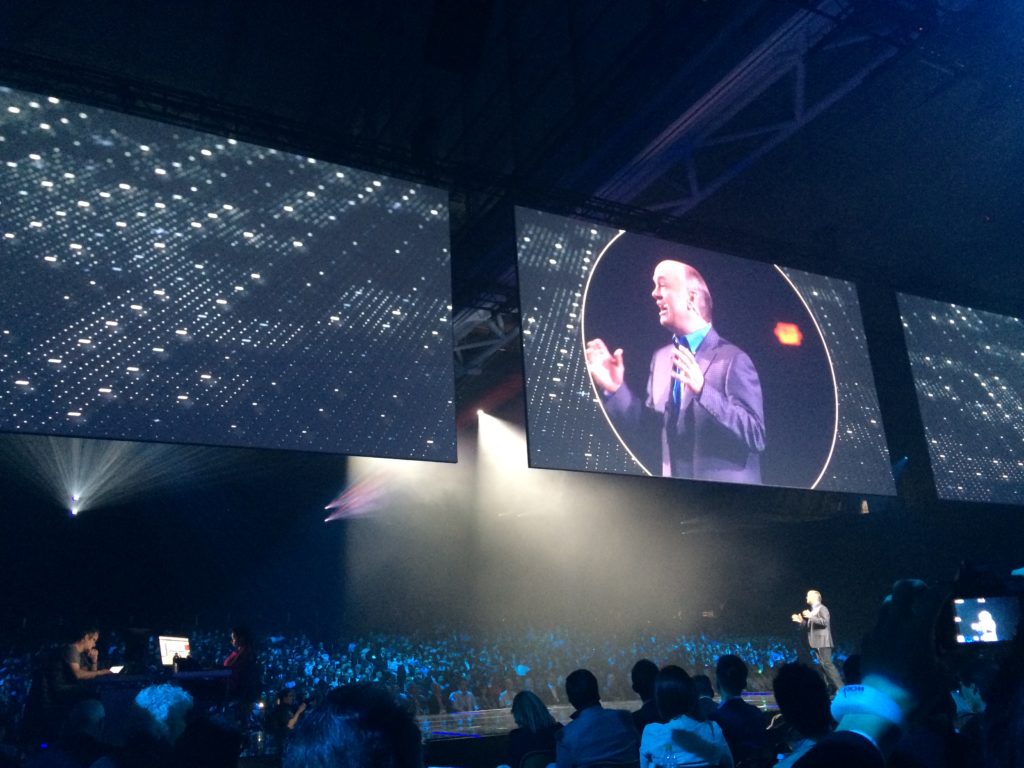
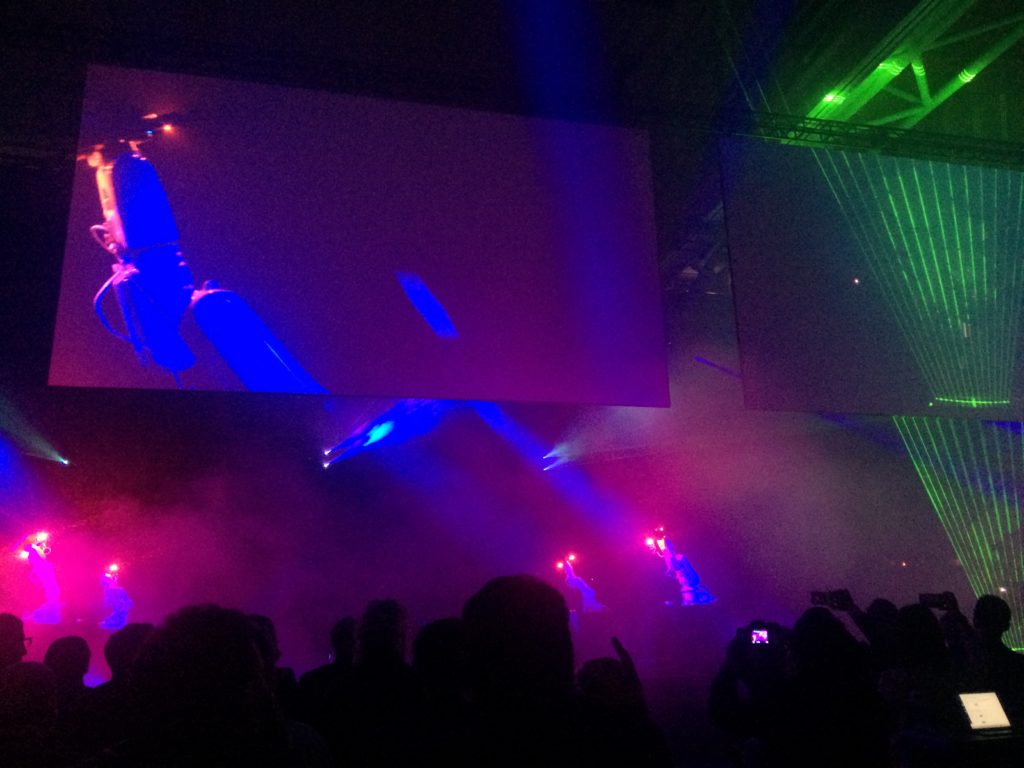
The era of living products
One industry that is being particularly impacted, is manufacturing. Data can be collected via the IoT or Industrial Internet of Things (IIoT) and analysed to optimise the manufacturing process.
The IoT provides manufacturers with the ability to take real-time data from physical products currently in service and use it to improve products that are currently on the line. ‘Simply’, the IoT allows manufacturers to use data from the field to see how a product is working: the physical/digital convergence.
>See also: How big data and analytics are fuelling the IoT revolution
This ability to digitally monitor a physical product and produce its ‘digital twin’ takes the friction out of engineering, by significantly reducing costs and increasing the rate of innovation simultaneously. Access to this real-time visibility inevitably leads to improvements in design, operation and service, and ultimately, provides the stepping stone to Industry 4.0.
Industry 4.0
Industry 4.0 combines the use of emerging technologies like AI, robotics and smart manufacturing. As hardware becomes a more simple husk, it is the software of these emerging technologies that provide the connective tissue for increased value creation. These technologies are transforming the industrial landscape, said Eric Schaeffer, senior managing director at Accenture during a panel discussion on Industry 4.0 and the transformation of manufacturing at LiveWorx.
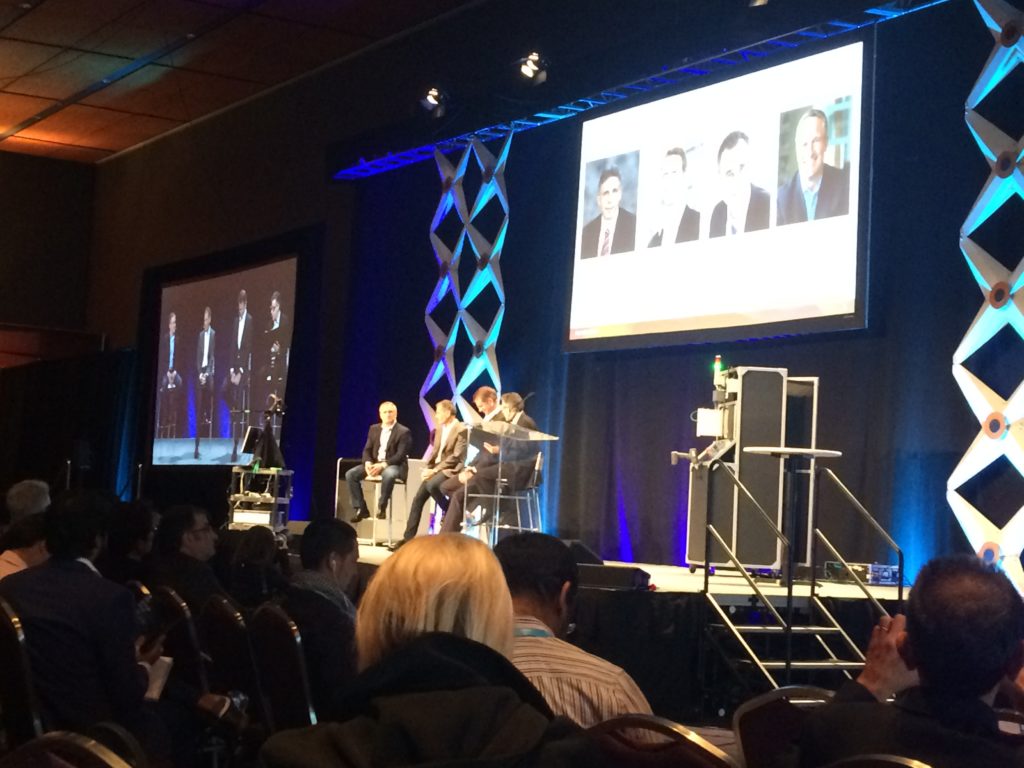
But how can manufacturers and enterprises adapt to this new technology as it emerges? In order to utilise the ever-increasing influx of data generated by the IoT, industries must be able to turn it into actionable, intelligent and intentional insight to improve efficiency and drive innovation.
>See also: The Fourth Industrial Revolution: Technology alliances lead the charge
At the moment, however, traditional manufacturers are only able to process and benefit from 1% of the data generated from these smart devices. Existing infrastructure within the manufacturing industry, explained Howard Heppelmann, divisional vice president and general manager for Connnected Manufacturing at PTC, is not designed to work together. The built-up, siloed systems get in the way of analytics and hinders the speed and agility required to innovate. So, how do companies increase their analytics capability and generate value from this?
The IoT platform
PTC’s IoT manufacturing platform, ThingWorx (version 8 available in two weeks) offers a solution to this industry-wide problem, connecting manufacturing data to the clients. The platform as an idea, brings in AR, analytics, big data, mobile, cloud, application enablement and connectivity. And according to a PTC developer, this integrated set of capabilities can work from any data source.
The new version allows customers to achieve faster and easier access to the IIoT devices and their data, retrieve this data from cloud service providers and analyse that data. e.GO, an affordable electric car manufacturer, told the audience at LiveWorx that without the visibility this platform provided, affordability of its product would have been difficult.
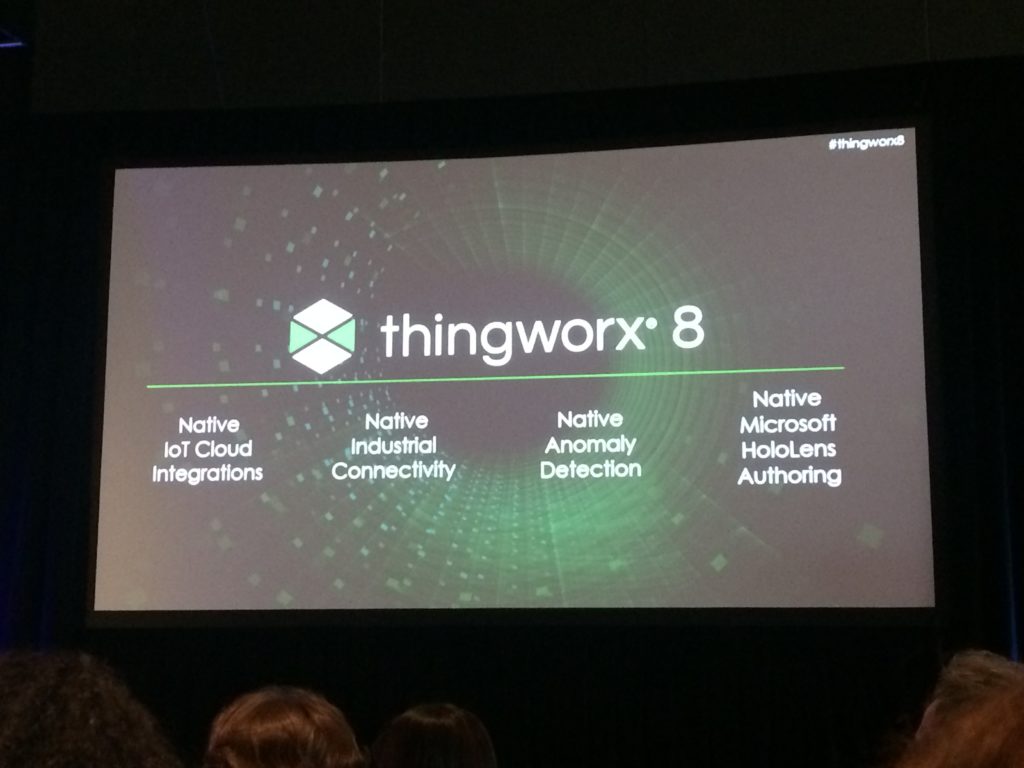
Perhaps the greatest asset offered by engaging the IoT effectively for manufacturers is this ability to produce virtual mockups, or the ‘digital twin’ of physical products with the use of augmented reality (AR). It speeds up the development process and in turn cuts costs.
Indeed, as Jim Heppelmann stated, ‘AR is a wonderful companion to the IoT’. It creates a hands on, visible and real-time view of a physical product in a digital space that transcends distance and time. AR needs data, and the IoT provides this missing link, which leads to the next generation of product lifecycle management (PLM).
>See also: The Internet of things will create endless opportunities for the enterprise
The creation of hands free AR experiences and the growing scale of capabilities offered by 3D printing will revolutionise the manufacturing supply chain. But it all hinders on the use of data being generated by the IoT.
It should be noted that currently, 70-80% of value – according to Schaeffer – is being generated by the digitisation of internal and external operations. Not from internet-connected devices. As businesses transform and recognise new opportunities, this value pendulum will certainly swing.
Ultimately, connecting smart products with platforms and analytics is necessary to truly instigate digital transformation of services via the IoT. Success in this ambition and necessity will bring new levels of efficiency, heralding in the Industry 4.0.
The UK’s largest conference for tech leadership, Tech Leaders Summit, returns in September with 40+ top execs signed up to speak about the challenges and opportunities surrounding the most disruptive innovations facing the enterprise today. Secure your place at this prestigious summit by registering here