The ‘Right to repair’ movement across Europe and the US is growing teeth. It has been building for the last few years in response to a number of factors: the growing e-waste problem, which has increased by 21% in five years; changing customer expectations and preferences around speed and cost of service; and of course, the large amount of money to be made in service that the OEMs want to keep captive. The European Union and US states, such as California and Massachusetts, among others, are starting to enact laws that will force manufacturers to enable end-users of their products to be able to repair faults – for up to 10 years in many cases – or select their medium of repair.
While on the surface at least, this makes a lot of sense, there are some more greyish areas where this might not be such a good idea, especially within industry. One of the most cited examples in right to repair campaigning is Apple, which restricts end-user repair through warranty terms and conditions, as well as making it physically difficult to access parts (in fairness, Apple does have a significant service ecosystem, and has extended service capabilities to an expanding portfolio of partners, but you get my point). From a consumer perspective, there is a lot of logic to being able to repair and not get caught into a manufacturer-induced upgrade cycle.
For industry though, other factors come into play, and we must be careful that we don’t get too carried away with what the law will enable organisations to do. There are some examples of industries, such as healthcare, where limited access to self-repair sometimes slows down the ability to have functioning equipment – one report suggests it has made hospitals’ reactions to the COVID-19 pandemic difficult due to slow ventilator repairs. However, it is important to remember that many field service teams are built on product expertise for a reason. For example, it is vital that certified technicians touch medical equipment to ensure patient safety.
Cloud data and security — what every healthcare technology leader needs to know
The field service market has evolved and continues to evolve to meet the needs of end users and not all manufacturers and suppliers have pursued a closed shop. Service teams themselves are changing, adopting more efficient digitally led practises to improve service times, repair accuracy and minimise downtime. There are also increasing trends in self-service provision, enabling end user teams to carry out minor maintenance jobs themselves, through self-service portals set-up by suppliers.
This is part and parcel of the servitisation trend, where traditional ideas of product ownership, service and product replacement are being re-worked. More and more organisations are looking at selling ‘outcomes’ and not products, and in many cases, service is built into the deal to ensure consistency and to guarantee those desired outcomes. For some organisations, right to repair could potentially undermine this and put the control of end user outcomes in jeopardy.
Some organisations might lose control of the outcome, whereas others might now see increased responsibility for the outcomes, but would want to find the most efficient way to deliver those outcomes – whether via the customer, remote, third party, or technicians. A service company, on the other hand, would want to drive that outcome, but it may not be feasible to do so effectively using their own workforce. The truth is multiple personas will have to touch the equipment asset – from self-service to remote support, to third parties. And it’s worth remembering that right to repair isn’t just for customers to self-repair – it’s also for them to choose who gets to perform the repair.
5G and manufacturing: the missing link to drive industry 4.0?
Can you fix it?
Of course, for end-users, this is their prerogative. As a report last year on John Deere revealed, farmers in the US were demanding the right to make basic fixes to their own tractors by getting access to the software that runs the machines, so they didn’t have to take them back to the dealer every time for a minor fix. John Deere, like many vehicle manufacturers, uses remote software updates to upgrade machine performance by fixing bugs or improving diagnostics. This is more of an argument about ‘pimping’ machines than actual fixes, but it raises the issue that if farmers are allowed to access the software, who actually changes the code and what does this mean in terms of warranty and ownership? A vendor can surely no longer offer warranty for third party errors, should they occur?
What it may mean is that right to repair could fuel a growth in third party fixers which would compete with vendors’ own service teams. Or it could be that vendors try and increase the breadth of approved third-party service agents, but this will take time and investment from all sides. When it comes down to it, it’s still about managing customer expectations on fixing equipment.
Whether the customer has the right to repair or not, the same principles remain – users want to avoid any downtime due to machine failure and they want to spend as little money as possible on parts and service. They also want to be able to do their own basic repairs where possible, guided through self-service capabilities, to avoid unnecessary service times and engineer journeys. This may have longer term effects on how machines are designed and constructed. We may see more self-contained parts that are easily swapped out by users and vendors creating ecosystems to give users a choice of approved parts and third-party service teams.
Ultimately, none of this undermines the core competencies of modern, digitally driven service. Right to repair underscores the importance of field service efficiency. While predictive maintenance will continue to evolve into a mainstay of machine servicing, right to repair could make manufacturers rethink product design, how parts stocking levels are determined, how they construct contracts, design and deliver virtual services and set-up third party service channels. For field service teams, it should be business as usual, at least for the short-term. In the longer term, no one really knows yet, but from a strategic perspective, servitisation and right to repair are two trends that are bound to overlap and drive critical decision making.
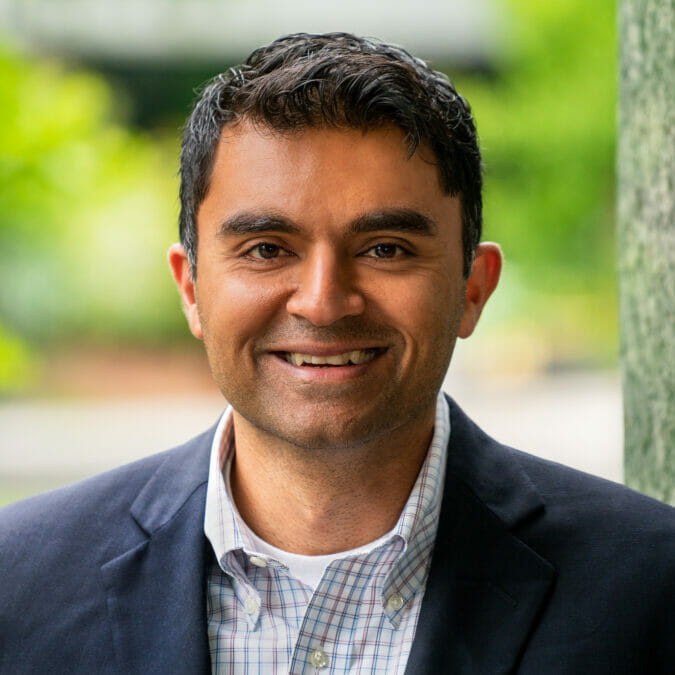